Composite Microwave Filters
Learn everything you need to know about composite microwave filters!
The Quantic Corry team loves sharing knowledge with our fellow electrical engineers. That’s why we have just developed a new comprehensive guide we think you will find interesting and helpful. If you are in need of high-quality composite cavity RF filters, we can help! We have a complete line of these filters in stock, ready to ship.
Our guide, Composite Microwave Filters, is completely FREE and full of great information, including:
- The challenges faced when developing these types of filters
- How to reduce the weight of any filter
- The benefits of using our brand of composite cavity RF filters
- The composite material used by Quantic Corry
Composite Microwave Filters
Download Now
Introduction
There has been a shift away from metal enclosures, which includes RF filters, to lighter weight composite materials. Historically, cavity and other styles of RF filters were manufactured out of aluminum because weight was not an issue. However, today, with the use of unmanned aerial vehicles and the need to conserve fuel usage, weight is considered on all components that are used to build the UAV. Therefore, Quantic Corry has developed their line of compositive cavity RF filters.
The Challenges
There were several challenges to developing composite cavity RF filters, including:
- Finding a material that could be CNC machined.
- Finding a material that was both silver and gold plateable with good adhesion.
- Finding a material with similar thermal expansion coefficients to aluminum.
- When there is a chance that the plating can wear off or thin, the composite material needs to be made of a material with the tensile strength that allows for the metal inserts to be pressed into the material.
The weight of any filter can be reduced by enclosing it in a composite instead of a metal. The real weight savings comes with larger filter types because large filters can generally handle more power and have lower insertion loss for a given rejection specification. Larger filters also generally perform much better than smaller ones.
The elements that make up filters at microwave frequencies are often distributed elements. The distributed elements mimic the performance of lumped element capacitors and inductors to create a working filter. Typical examples of distributed elements are open or shorted transmission lines arranged in specific relationships to each other with carefully calculated lengths and spacings. Distributed elements are mostly metal elements separated by dielectric materials, such as air, Teflon, or pcb laminates. These distributed elements are usually larger than the lumped element inductors and capacitors that are often associated with the typical filter.
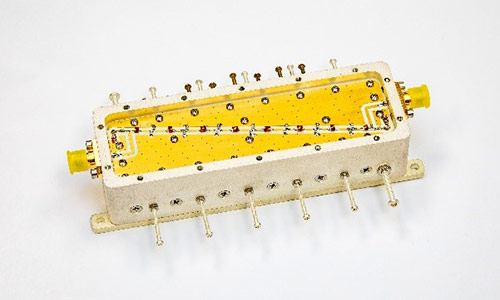
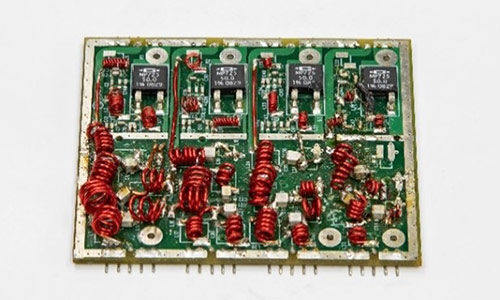
Filters providing the lowest insertion loss for a given rejection requirement are usually bigger, and therefore, they are heavier than lower performing filters. Unless insertion loss can be increased or rejection decreased, a filter can be only so compact. The reality is that allowing internal elements of the filter to increase in size reduces the loss of each element, which contributes to improving overall loss.
With increased size, comes increased weight. If the metal of the filter housing and the internal filter distributed elements could be switched over to a lighter weight material with the conductivity of a good metal conductor, the weight will decrease without decreasing performance. Composite materials are non-conductors that weigh less than aluminum, brass, copper, and other metals typically used in filters.
Using the composite as the base material and plating the composite with a good conductor, such as silver, combines the low-loss advantages of a distributed element with lower weight. Note that size is not affected though.
The composite material used by Quantic Corry is about one-half the weight of aluminum. The composite that we chose for our product line is called Ultem®, which is also the brand name for polyetherimide (PEI). It is an amber, transparent high-performance polymer, which combines high strength and rigidity at elevated temperatures with long-term heat resistance.
The ULTEM® Resin family of amorphous thermoplastic polyetherimide (PEI) resins offers outstanding elevated thermal resistance, high strength and stiffness, and broad chemical resistance. ULTEM® is available in transparent and opaque custom colors as well as glass filled grades. Plus, ULTEM® copolymers are available for even higher heat as well as chemical and elasticity needs. ULTEM® resins uniquely balance both mechanical properties and processability, offering design engineers exceptional flexibility and freedom.
Ultem® excels in hot air and water. It is hydrolytically stable and retains 100% of tensile strength after 2,000 steam autoclave cycles at 270°F. Ultem® also retains 85% of its tensile strength after 10,000 hours of boiling water immersion and is UV and gamma radiation-resistant.
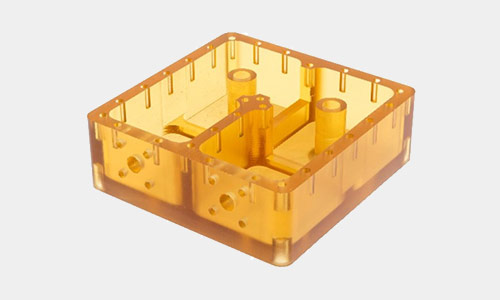
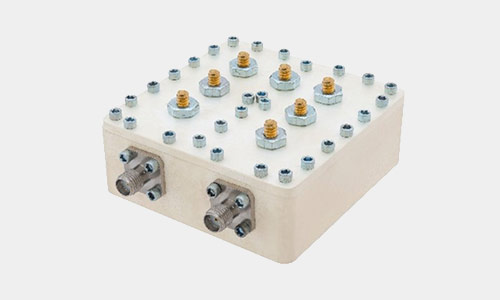
Filters are not comprised solely of aluminum, so a total weight savings of 50% for the entire filter is unrealistic. The weight of the RF connectors, the screws holding the unit together, any insulators, such as Teflon, all contribute to the overall weight of the filter. It is possible to get as much as a 30-40% weight reduction.
Weight Comparison Example
This model is for a 2.2 GHz, 6 Pole Bandpass Filter w/ Type N Connectors
Filters are just one example of how composite materials can help to reduce weight. Any application that requires a shielded enclosure can benefit. The material can be machined into virtually any shape, including the typical box used to house electronics sub-assemblies or circuit boards. The composites can be plated to form a Faraday shield for all of the typical reasons electronics are housed in metal enclosures (emissions, susceptibility, and protection).
Since the plating of the composite material is more delicate than the plating on metal structures, our designs also incorporate protective mechanical features to avoid any disruption in the plated surfaces that are important to the function of the component. For example, if the unit requires a good ground connection, the mounting points of the component will have threaded inserts, or helicoils, installed so that the mounting of the unit will not destroy the plated connection. For thru hole connections, we recommend using flat washers that have direct contact with the plated surfaces. This allows for the application of non-rotating, even pressure when mounting the component.
The temperature stability of composite materials is a consideration when designing filters that often have tuning elements that are very sensitive to physical positioning. Much of this concern can be eliminated by using composites with thermal coefficients of expansion that are almost identical to aluminum. Precision filters can be produced that are very stable over industrial temperature extremes.
Composite materials do not conduct heat well, certainly not as well as a typical metal. Fortunately, the surface plating can provide a path for efficient heat conduction to radiating and/or heat conducting surfaces outside the enclosure. This is usually sufficient for moderate heat generated inside the enclosure. At higher levels, the composite may need to be combined with selected solid metal parts to remove the heat.
In machining terms, literally any item that can be made out of aluminum, can be made with our composite material. The composite material we use is ultra-machinable. It does not require any special cutting tools. 2D and 3D features are all possible with this material, allowing all the different microwave bandpass and multiplexer filter designs to be made, including cavity, tubular, comb, and helical types. The Ultem® composite is readily available from a variety of domestic sources, and it is available in plate sizes 24” x 48” and 4” thick.
It is also available in a variety of rod sizes for lathe work. Rod sizes up to 12” diameter are available. These available sizes make it particularly interesting when looking for filters of low to very low frequencies, where the size of the overall cavities get very large. As noted above, some items can be made better by going bigger and still allowing for less weight. Additionally, items that are in use now can be duplicated using composites and made lighter, while maintaining the same performance.
Our base composite material is also moldable. For larger production requirements, where cost and weight are the most critical parameters, we can design and incorporate a molded housing design where the amount of the composite material is minimized rather than machined into scrap. This helps the cost of the finished unit both in material costs and machining time. Additionally, features that are not machinable can also be incorporated into the component designs. Molding of this composite material can be either through injection molding or extrusion. Oftentimes, a combination of molded and turned components can be used together to make the cost of the unit as optimum as possible.
In items that require a more stringent capability for tests, like shock and vibration, composite designs allow the designer to build in a more robust structure (oftentimes, meaning thicker internal walls or larger fastening hardware) without drastically increasing the overall weight of the unit.
Using our proprietary plating approach, we are able to supply these composite units with a variety of finishes. Our plating process incorporates multiple steps to assure the material is properly pre-conditioned to eliminate any stresses imparted to the composite during the plating cycle. It also incorporates a multi-step process to adequately prepare the composite surface for acceptance of the initial metal plating layer, which yields superior adhesion of the metal plating to the composite surface. In comparison, the adhesion of this metal layer surpasses most plating results on composite materials, where the plating can be removed by simply wiping it off. The final plating type can then be selected for performance and/or cosmetic reasons. Commonly we use silver for the final plating, and then we paint over the silver for corrosion protection. But, we can also provide these units with other finishes as well, like gold (if the end user prefers a non-painted unit) or tin (if it is for a more general purpose item, and cost is the more important factor).
The composites we use are well suited for both commercial and military temperature ratings up to 125°C. They also have an excellent water absorption capability, making them suitable for “wet” environments and excellent for chemical resistance. Ultem® is an inherently flame retardant, low smoke resin, and it has UL 94-VO, V2, and 5VA ratings. Ultem® is also a RoHS compliant material.
Author Bio
Robert Meilleur has a BSEE degree from the University of Arizona. From 1987 to 2002, he was a Design Engineer and Engineering Manager for Tusonix, Inc. In this role, he specialized in EMI/RFI filtering products and solutions. In 2002, he joined the Quantic Corry team, where he became the VP of Operations.
Author Bio
James Price received a BS degree in Electrical Engineering from West Virginia University in Morgantown, WV in 1983. From 1985 to 1995, he was an engineer specializing in communications with RCA which eventually became Lockheed-Martin in Camden NJ. From 1995 through 2004 he designed CATV products for Tollgrade Communications, Cheswick, PA.
He is currently VP of Engineering for Quantic Corry, Warrendale, PA. His areas of focus include RF and microwave filters, multiplexers, switches and antennas.